На птицефабрике "Рефтинская" внедряют инструменты бережливого производства.
К нацпроекту "Производительность труда и поддержка занятости” присоединились уже более семисот предприятий страны. В их числе - ОАО "Птицефабрика "Рефтинская".
"Майским" указом президента России поставлена цель - выйти к 2024 году на уровень роста производительности труда в базовых несырьевых отраслях экономики не менее чем на пять процентов в год.
- Наша задача - помочь предприятиям, участвующим в нацпроекте, "прыгнуть выше головы", выйти на новый уровень эффективности, обеспечить стабильный рост производительности и конкурентоспособности, - объясняет генеральный директор Федерального центра компетенций в сфере производительности труда (ФЦК) Николай Соломон. - Центр располагает обширной экспертизой в различных отраслях экономики, что позволяет нашим специалистам делиться опытом,передавать инструменты бережливого производства бизнесу. Благодаря этому будет создана экосистема для запуска цепной реакции роста производительности как в рамках одной компании, так и по всей стране в целом.
Полгода пилотный проект реализуется в ОАО "Птицефабрика "Рефтинская". За это время здесь удалось почти в 2,5 раза увеличить выработку одного оператора на участке полуфабрикатов из цыплят-бройлеров. До прихода экспертов ФЦК здесь даже рассматривался инвестиционный проект, за счет которого должна была повыситься производительность одной из линий. Однако выяснилось, что загрузка не составляет и тридцати процентов, поэтому было решено повышать эффективность за счет использования внутренних ресурсов, без дополнительных инвестиций.
Например, раньше на участке наблюдались ежедневные 20-минутные простои. Рабочая группа компании предложила ввести специальную доску заказа сырья. На ней операторы линии указывали, какое сырье и в каком количестве нужно доставить. Тогда водитель погрузчика доставлял сырье вовремя и только в необходимом объеме, тем самым избегая скопления излишков.
Кроме того, в зонах хранения была введена специальная визуализация: благодаря использованию цветных маркеров стало понятно, где находится то или иное сырье или инструменты. Это существенно снизило время, которое раньше уходило на поиск нужных инструментов, а также помогло своевременно пополнять запасы, чтобы потом не останавливать линию из-за нехватки сырья.
Эксперты также отметили, что из-за нерационального расположения напольных весов погрузчик тратит лишнее время на перемещения. Перестановка этих весов - вкупе с другими инструментами бережливого производства помогло сократить маршрут водителя на 42 минуты в день, что позволило ему быстрее и чаще транспортировать сырье к рабочим зонам.
Производительность линии также существенно увеличила установка стоповой кнопки и роликовых направляющих для укладки тушки на лоток в процессе фасовки. А когда эксперты просто изменили схему позиционирования тушки на лотке, выработка увеличилась более чем в два раза.
В результате реализации пилотного проекта время протекания процессов сократилось на 28,5 процента, выработка высокомаржинальных продуктов выросла на 243 процента. Теперь на одного сотрудника в час приходится 175 упаковок продукции, а не 72, как было раньше. При этом загрузка операторов на участке в течение дня стала более ровной, отпала необходимость в сверхурочной работе.
Е. Лобова,
"Асбестовский рабочий"
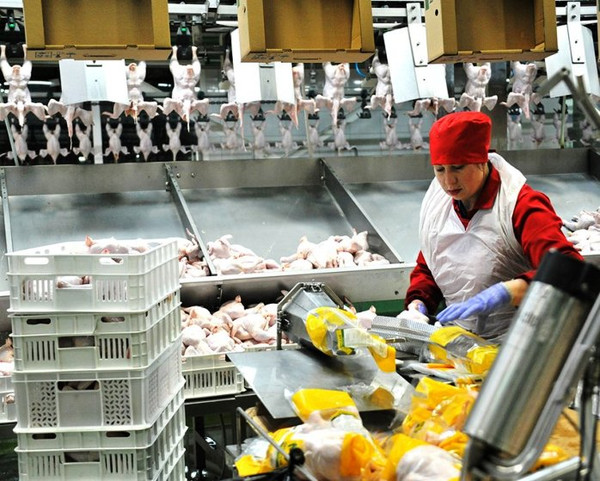 |